A Lesson in Heat Transfer
By Andrew Wiehebrink, R&D Spirits Division
“Assume a spherical cow”
Before I came to ISC to study spirit maturation, I was in the field of engineering. I graduated with a degree in Mechanical Engineering and for the first five or six years out of college, I was strictly focused in that area. In college, my main interests were in heat transfer and fluid dynamics so that is what I wanted to be involved in as I began, what I thought was going to be, a lifelong career in the field of engineering.
A lot of what I did out of the gate was strictly pen to paper math-based quantifications and predictions for various applications. It doesn’t sound exciting, but working with the laws that govern heat, air, and fluid flow to solve problems proved to be interesting and I learned quite a bit. As time went on, I moved to design and new product introduction which was a lot more fun. Eventually, I decided to put my engineering days behind me and pursue a career in the spirits business.
I still see a lot of those old engineering principles are at work inside the cooperage so I thought it would be fun to explore a few of them and apply them to everybody’s favorite part of making barrels…CHARRING! More specifically, let’s take a look at how the ambient temperature in the cooperage affects the charring process.
THE PLANE WALL
One of the simplest problems with one dimensional steady state conduction is the plane wall. You have a fluid at ‘x’ temperature on one side of a piece of material, and another fluid at ‘y’ temperature on the opposite side of the material. Given what we know or what we don’t know about the variables in the scenario, we can solve for a number of different things. One of the more useful being heat flux, or how heat moves through an object or material.
How heat moves through the barrel staves is of particular interest in many parts of the barrel making process. Curing, toasting, and charring just to name a few. How deep do we want the toast profile to penetrate the stave? How much transformed wood do we need for whiskey that will be in a barrel for a matter of weeks versus a matter of years? All of which deal with some facet of one-dimensional conduction.
As the ambient temperature in the cooperage changes, it may be helpful to determine if we should adjust the length of the charring cycle. There are a couple of different factors to consider here but first, let’s just see how the temperature of the air moving around the barrel during charring comes into play.
Ultimately, we are looking for a change in heat flux as a function of the outer fluid temperature. In the case of this example, let’s assume a 350 F difference between the hot summer days in the cooperage and the cooler winter days (1000 F vs 650 F).
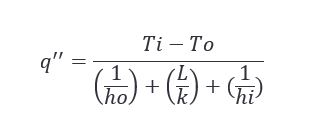
Working with the parameters described in the appendix (located at the bottom of this post), we can expect to see the heat flux change with respect to the ambient air temperature as follows.

Given these results, I think we can safely say that all things considered, ambient temperature could have a measurable effect during the charring process. The caveat is that the effect doesn’t produce a large enough difference to warrant changing the length of the char cycle to accommodate for said effect. For two reasons…
- The charring process is very short. I think this is the key factor here…
- Possibly if the inside of the barrel was much cooler and the heating process was extended? Perhaps if we applied these calculations to the toasting process the effect might be more impactful.
- Being that the air temperature inside the barrel is so hot during charring, the small difference in ambient temperature between summer and winter probably isn’t significant enough to have an effect across the thick, insulating material (oak).
Knowing the heat flux allows us to solve for a couple more things that might help us in making our conclusions. Looking at the inside surface temperature during charring could be interesting and we can do that by applying the following equation.
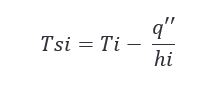
Plugging in our newly calculated q’’ values for summer and winter in the above equation, we get the following results.
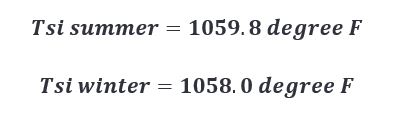
This doesn’t appear to be a large enough difference to warrant any change.
HEAT CAPACITY and NEWTON’S LAW OF COOLING
Looking at the conditions that exist before an event occurs can often be useful in solving many problems tied to said event. The temperature of the barrel before it goes into the char fire will likely have a measurable effect on the accuracy of the char level, but like the last example, we will need to apply a couple handy formulas to determine if it is significant. The equation we will want to keep in mind is below. This equation actually shows up frequently not only in manufacturing, but also in maturation. It governs quite a bit.
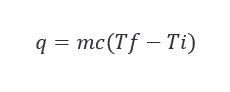
For our application, this translates to the amount of heat required (q) to get the oak staves to a temperature necessary to ignite is equal to the mass of the oak staves (m) multiplied by the specific heat of oak wood (c) multiplied by the difference between the ignition temperature and the temperature at which the barrel enters the char station.
As the barrel exits the dry fire, it begins to cool down as it heads for the char fire. And it continues to cool until it reaches the point where it enters the charring station, and the flame is initiated. Before solving our problem, we need to calculate the temperature of the interior surface of the barrel at that point in both summer and winter. Newton’s Law of Cooling works great for predictions similar to this.
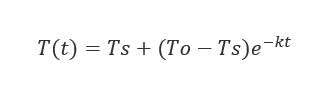
This tells us that the rate at which a body cools is directly proportional to the difference between the body and its surroundings. This confirms that the ambient temperature will have some level of effect on the accuracy of the char but again, we need to determine if it is significant or not… First, we need to do those cooling calculations and for that, we are going to make a few assumptions…
- The temperature of the barrel is 3500 F once it comes out of the dry fire.
- There exists a 300 second delay between dry fire exit and the char station.
- Convection coefficient is approximated and assumes no flow in the cooperage.
- Assuming same ambient temperature difference as the previous example.
- 1000 F summer
- 650 F winter
As such, temperatures of the interior surface of the barrel at time of char are approximated below.
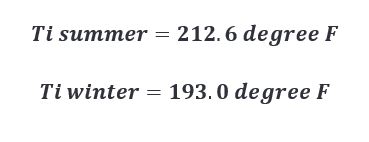
Setting up our heat capacity equations for each scenario we then calculate the following.
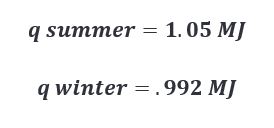
In reality, the amount of heat required to ignite the barrels would be less than the values above because ignition doesn’t require the entire mass reaching a specific temperature. However, for our purposes in this example, we can still make an accurate decision as to whether or not we need to adjust our charring process. If the mass is reduced by a common factor, it should not affect the conclusion.
Assuming the calculations above are accurate (I am not an engineer anymore so I have the luxury of being able to make no guarantees), it takes about 6% more energy in the wintertime to get the interior surface of the barrel to a temperature where it can ignite. Assuming a 55 second charring cycle, we would have to increase the cycle by a little over 3 seconds (or adjust the intensity) to account for the cooler temperature!
And that is exactly what we do! The operator will adjust the char time each day based on the changes in ambient temperature inside the cooperage. Hopefully this lends validity to one of my favorite ISC taglines… ”Charred to Perfection!”
Cheers!
Andrew
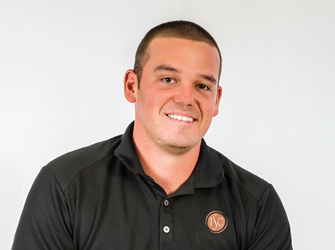
APPENDIX
Oak Assumptions
Ignition temperature = 5500 F
Mass = 34.24 kg
Density p = 590 kg/m3
Thermal conductivity k = .16 W/m*K
Specific heat c = 155 J/kg*K
Environmental Assumptions
Inside barrel air temperature = 14000 F
Summer ambient = 1000 F
Winter ambient = 650 F
Convection coefficient inside barrel = 130 W/m2*K
Convection coefficient outside barrel = 30 Wm2*K
Comments 1
I am sure that this will be a “rolled eye” article for most, but as a retired chemical engineer, I enjoyed it quite a lot. So thanks for being game to scare most and give something of a technical bend to those of us who enjoy this!